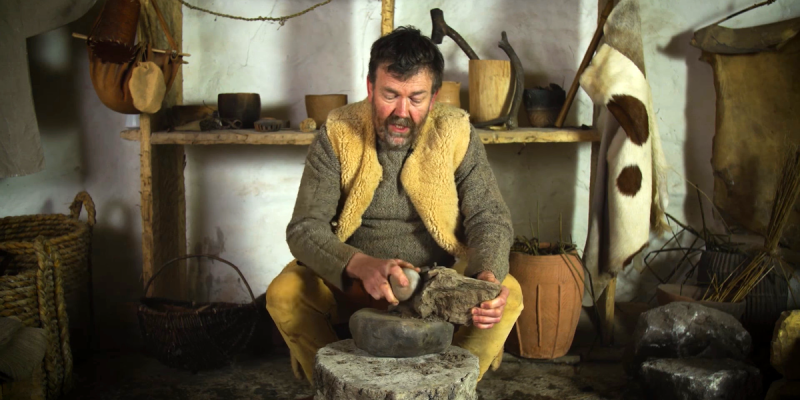
It isn’t an uncommon science fiction trope for our hero to be in a situation where there is no technology. Maybe she’s back in the past or on a faraway planet. The Professor from Gilligan’s Island comes to mind, too. I’d bet the average Hacakday reader could do pretty well in that kind of situation, but there’s one thing that’s often overlooked: materials. Sure, you can build a radio. But can you make wire? Or metal plates for a capacitor? Or a speaker? We tend to overlook how many abstractions we use when we build. Even turning trees into lumber isn’t a totally obvious process.
People are by their very nature always looking for ways to use the things around them. Even 300,000 years ago, people would find rocks and use them as tools. It wasn’t long before they found that some rocks could shape other rocks to form useful shapes like axes. But the age of engineered materials is much younger. Whether clay, metal, glass, or more obviously plastics, these materials are significantly more useful than rocks tied to sticks, but making them in the first place is an engineering story all on its own.
Wood, Mud, Clay
The first steps were using wood from trees, including bark and unusual wood like cork, and other plant materials. They used mud, too, and mudworking evolved into ceramics about 26,000 years ago. Pottery was high science in its day. The Corded Ware culture, who spread across Europe around 5,000 years ago, created pottery that they would decorate with rope while it was still wet. When fired, the rope would burn away and leave its imprint in the finished piece. Bone was another early structural element. People today sometimes mimic prehistoric pottery techniques, like the stone-age tech video below.
Copper Days
When the first people stumbled into copper in its elemental form, around 7,500 years ago, people started to shape it into useful implements. About 500 years later, there is evidence people learned to melt copper to help with the shaping process. It would be another 1,000 years before craftsmen started melting copper and casting it. Copper is soft on its own, but by experimentation or accident someone figured out that adding arsenic to copper would make bronze, which was much harder. Even a half percent of arsenic can make a bronze that is 10% harder and stronger than elemental copper. Bump that two percent and the results are even better. Later bronze formulae would employ tin in place of the arsenic, but tin would have to wait for more advanced metallurgy. It took over, though, not because it is much better from a metallurgy standpoint, but smelting and casting arsenic is bad for your health.
Since copper ore often has arsenic in it anyway, this bronze discovery was easy to make. Bronze was used extensively in Europe, Asia, Africa, and South America at different times in the distant past. If you have the gear, you can make your own bronze like [Paul] does in the video below. You probably even already have the solder he uses.
Beyond Bronze
Metals beyond bronze would have to wait until about 5,000 years ago when ironworking is thought to have started in earnest, coexisting for a time with bronze, and then eventually replaced by steel.The Iron Pillar of Delhi is the oldest surviving example of corrosion-resistant iron. The pillar is over seven meters tall and is about 1,600 years old. While people in Persia and India learned to create steel, its production was highly specialized and steel wasn’t widely available until the 1800s.
Although the pyramids in Egypt and Central America are impressive, the Greeks and Romans really had a handle on material sciences. It didn’t hurt that the Romans had soil that made it easy to create concrete. The Greeks knew about asbestos and used it for clothing and tablecloths. The upside was to clean them you simply threw them in a fire. The downside was that scholars noted that the slaves mining asbestos didn’t live very long.
Real Engineered Materials
Probably the closest we had to an engineered material for many centuries was glass. Glass has a surprisingly long history. Glass can occur naturally around volcanos and when lightning strikes sand, but it was relatively rare making it very valuable. Archeologists think that glass production started in northern Syria, Mesopotamia, or Egypt. Egyptian glass dates back to about 3100 BC. Molded glass appears in Syria around 1500 BC. Keep in mind there was no Internet and making glass was a closely-guarded secret. By 650 BC, though, a manual was written in cuneiform describing how to create glass. Nearly six centuries later, the Babylonians figured out how to blow glass.
Many people who worked glass didn’t actually make it but acquired it premade as beads, rods, or ingots. Glass ingots have been found onboard ancient shipwrecks such as the Uluburun shipwreck off the coast of Turkey. The 175 colored ingots are the oldest known. Interestingly, the ship also carried a jar full of glass beads along with other raw materials like ten tons of copper and about a ton of tin. This would be sufficient to create about 11 tons of bronze.
One of the great things about glass is that can be heated and remade. This is good for recycling, too, of course. The hotter the glass, the less viscous it is. That means that you can heat glass up to make it very amenable to reshaping and then as it cools you can do more precise manipulations on it as the viscosity decreases.
Romans really had glassworking down pat. You can see a recreation of how they made glass pieces in the video below.
Starting about 25 AD, glass really took off. Within a century, it became relatively affordable. This is about the same time people figured out that adding manganese dioxide to glass would render it clear and, as mentioned earlier, the Babylonians learned to blow glass, making production of glass vessels cheaper than many alternatives. Window glass was very poor quality at this time, however.
More Modern Glass
It would be 1674 before George Ravenscroft discovered that adding lead oxide to molten glass made it easier to work and improved the finished appearance. The idea that glassmaking is so old is incredible when you realize that it requires temperatures of around 1700 °C. Today that’s not a big deal, but imagine building such a furnace thousands of years ago, or on that alien planet you are stranded on.
Modern commercial glass uses soda ash to lower the melting point. However, glass made with soda ash had an unfortunate tendency to melt in water. The inclusion of limestone creates soda-lime glass which handles water just fine. In addition, magnesium oxide and aluminum oxide make the glass more durable. The exact additives depend on the use of the glass. While pure glass — fused quartz — would be 100% silica, modern glass is about 70% by weight. There are other processes, too. Pyrex is a brand name for borosilicate glass which is made with boron oxide to give it excellent temperature resistance. Gorilla glass is well-known for durability in cell phones. You can see how that’s made in the video below.
Front of House
Modern glass factories usually have three distinct parts: the batch house, the hot end, and the cold end. The batch house handles the raw materials. As you might expect, the hot end melts down the sand and other raw materials to create glass. The cold end treats, inspects, and post processes the glass products.
Sheet glass is made using a float process. A metallic liquid — usually tin — holds the molten glass until it hardens. Tin works well because it has a high specific gravity and doesn’t mix with the molten glass. However, oxygen causes problems with tin dioxide production, so the process is usually done in a nitrogen atmosphere. This produces a very flat and uniform sheet. Prior to the invention of the float glass process, sheet glass was made by blowing cylinders, cutting them, and flattening them out, among other methods.
As you can imagine, this wasn’t very effective. The tin bath self-levels and the glass forms a perfectly smooth and evenly thick ribbon. As the glass flows, the tin bath’s temperature is cooled from 1100 °C to about 600 °C. Then the glass can be picked off with rollers. The speed of the rollers and the flow speed create different thicknesses of glass. Cooling through a special kiln anneals the glass and it is later cut into sheets of the desired size.
One Word… Plastics
We haven’t even gotten to plastics, but since most people know about them, that’s not a problem. Plastics as we know them date back to 1907, so they are in the same age bracket as radio and computers. Sure, there were some naturally occurring plastic materials or materials like rubber that could be processed into useful forms: mesoamericans, for example, used natural rubber for balls. Some early plastics were made from milk, which is a common science experiment for kids, even today.
The first synthetic plastic wasn’t bakelite, although that was the first fully synthetic plastic. The first was in 1855 when [Alexander Parkes] reduced cellulose with nitric acid to form Parkesine which saw some use as fake ivory. In the late 1800s, several milk-based plastics appeared. Widespread plastic use didn’t really start, however, until after World War I. Many common plastics like PET and polypropylene didn’t appear until the 1940s and 1950s.
Next Time
Next time you want to imagine being stranded on a low tech planet and setting yourself up as king, think about all the materials you take for granted as a citizen of a technological civilization. (And read the second book in Harry Harrison’s Deathworld trilogy for a more practical take on the scenario.) Wire, fasteners, pressure-treated lumber, sheet metal, plastics, adhesives, solder. We stand on the shoulders of giants so tall, we hardly notice they are there.
If you do find yourself on Harrison’s planet, maybe save time and just build a 3D printer. Then you can mold glass. But then you’ll need motors and controllers. That takes wire and metal contacts and resistors and… well… we didn’t say it was going to be easy. Then again, solar heat and sand can make glass without too much tech.
0 Commentaires