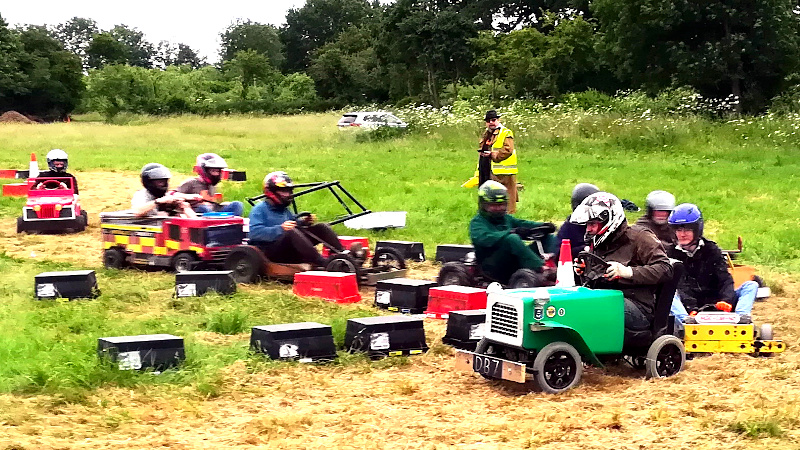
Four years ago when the idea of a pandemic was something which only worried a few epidemiologists, a group of British hardware hackers and robotic combat enthusiasts came up with an idea. They would take inspiration from the American Power Racing Series to create their own small electric racing formula. Hacky Racers became a rougher version of its transatlantic cousin racing on mixed surfaces rather than tarmac, and as an inaugural meeting that first group of racers convened on a cider farm in Somerset to give it a try. Last weekend they were back at the same farm after four years of Hacky Racer development with racing having been interrupted by the pandemic, and Hackaday came along once more to see how the cars had evolved.
Probably The Most Fun You Can Have With Five Hundred Quid
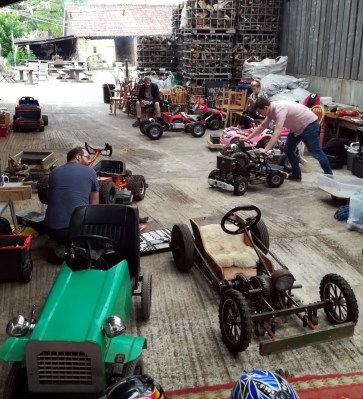
We’ve mentioned Hacky Racers and Power Racing enough that many readers may be familiar with them, but to recap, the rules governing the series specify a maximum length and width of 1500 mm and 900 mm, a 2-horsepower power limit enforced by appropriate fuses for the voltage employed, and a £500 (around $600) budget limit. In keeping with the Power Racing inspiration many of the vehicles sport creative bodywork designs, and the result is a field of cars with top speeds somewhere between 15 mph and 20 mph (around 30 km/h).
At those first Hacky Racer meetings back in 2018 there was a mixture of power plants. There were a few 24 V DC transaxles from mobility scooters, some DC power plants from golf buggies, and the faster vehicles featuring 2 hp brushless auto rickshaw motors. Most chassis designs were modified from donor machines, and motor controllers were commoditised Chinese modules. Thus it’s interesting to see how a few years of development has evolved the formula. Four years later the newer machines all have custom chassis designs, there were none of the mobility or golf-based DC motors on show, and the rickshaw motors have been joined by converted car alternators. It’s clear that it’s in these last power plants that the most development is proceeding, so it’s worth taking a closer look.
Pushing The Limits With The Cheapest Brushless Motor Of Them All
We covered the conversion of alternator to motor back in early 2020, and from that we know they require a DC bias for their field winding as well as the 3-phase AC from the motor controller. Experimentation has shown that this winding requires between about 2 A and 5 A depending on the alternator, but it’s in managing this figure that some of the most interesting technical developments lie.
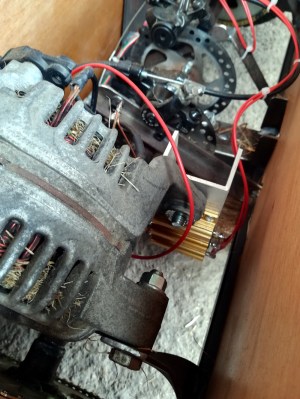
In a brushless motor the stator is a magnet, and it spins in a field created by a set of coils spaced around it. Like most smaller brushless motors the rickshaw motors have a permanent magnet as their rotor, which works well but is prone to overheating. The alternators have an electromagnet with a set of brushes as their stator, and this electromagnet forms the field coil. The more current in this coil the more magnetic field there is, and thus the more torque the motor can produce. More magnetic field also means more back EMF though, and since the motor controller must counteract this back EMF there’s a tradeoff in that the top speed is lower when the current is higher for more torque. The interesting developments with these motors therefore come with variable field current to select the desired combination of torque and top speed.
The simplest method for providing field current is to place a suitable resistor in series with the field coil and hook it up directly to the battery. This seems to be the preferred route of the moment, with one machine using a pair of relay-selected resistors for different motor torques switched in and out by means of a button on the steering wheel. This first-generation field control is being displaced by active electronics, with one racer using a small DC motor controller to power the coil and another experimenting with a buck converter that will eventually map the field current for the best torque at a particular speed.
It’s clear then that the Hacky Racers are pushing the development of their formula, and that they’re doing so while retaining the have-a-go character of the event is to their credit. Motorsport is blighted by so-called chequebook racers, and in this respect Hacky Racers join lawnmower racing as the antidote to formulas which take themselves too seriously. Meanwhile the development of car alternators as brushless motors has huge value for anybody experimenting with small-scale electric traction, so we look forward to more refinement of those techniques.
As we close this piece it’s worth mentioning the venue that hosted the Hacky Racers as they let their hair down. North Down Orchard is a working Somerset cider farm with camping facilities and an excellent cider barn. Some of us here at Hackaday are connoisseurs of good quality real cider, and we wholeheartedly enjoyed North Down’s cider as a particularly welly-crafted example of the art. We hope the Hacky Racers convene there again, and we look forward to bringing you whatever new technical advancements they’ve made in the intervening time.
0 Commentaires