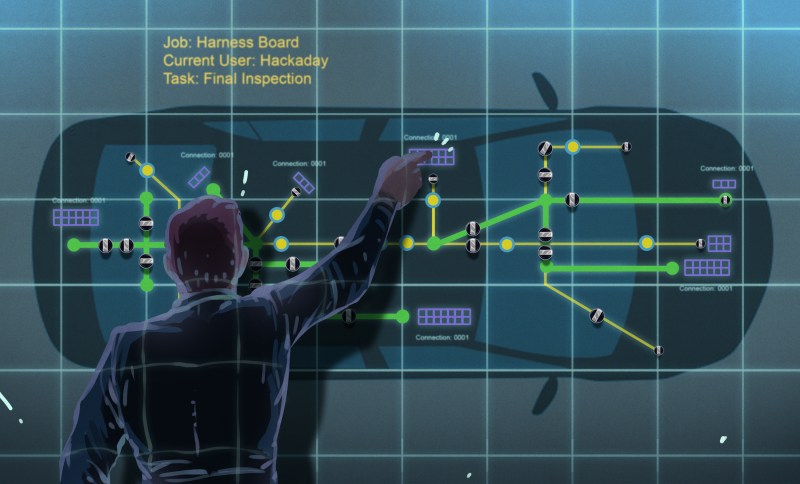
Even from the very earliest days of the automobile age, cars and trucks have been hybrids of mechanical and electrical design. For every piston sliding up and down in a cylinder, there’s a spark plug that needs to be fired at just the right time to make the engine work, and stepping on the brake pedal had better cause the brake lights to come on at the same time hydraulic pressure pinches the wheel rotors between the brake pads.
Without electrical connections, a useful motor vehicle is a practical impossibility. Even long before electricity started becoming the fuel of choice for vehicles, the wires that connect the computers, sensors, actuators, and indicators needed to run a vehicle’s systems were getting more and more complicated by the year. After the engine and the frame, a car’s wiring and electronics are its third most expensive component, and it’s estimated that by 2030, fully half of the average vehicle’s cost will be locked in its electrical system, up from 30% in 2010.
Making sure all those signals get where they’re going, and doing so in a safe and reliable way is the job of a vehicle’s wire harnesses, the bundles of wires that seemingly occupy every possible area of a modern car. The design and manufacturing of wire harnesses is a complex process that relies on specialized software, a degree of automation, and a surprising amount of people-power.
More Wires Than Ever
The idea for this article came from a conversation I had with Elliot Williams, and an off-hand mention of a chat he had with an engineer who makes software to design car wire harnesses. My first thought was, “There’s software to do that?” which was quickly followed by “Of course there’s software to do that!”. The wiring needed to run a modern vehicle is not something that can be done ad hoc — wire harnesses are highly engineered, both to handle the demands that will be placed on them electrically, and mechanically engineered to not only fit in the space available but to survive the rigors of perhaps several decades of use under challenging environmental conditions.
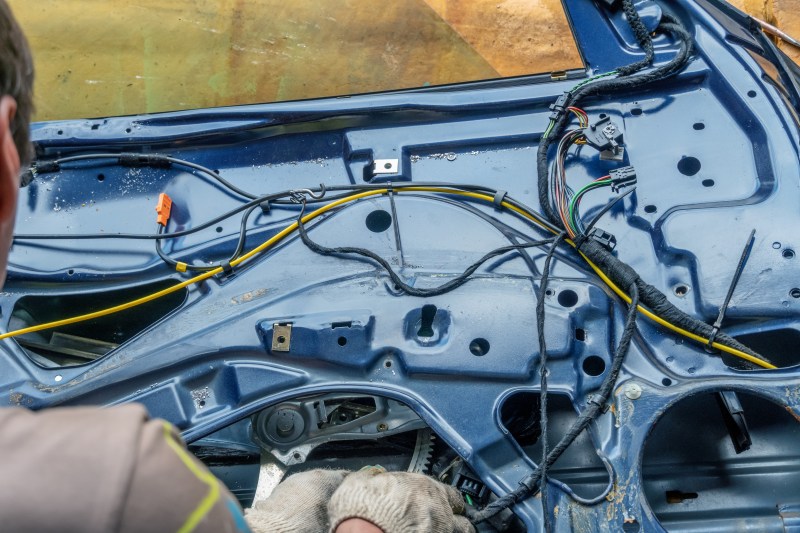
Wire harnesses also have to be manufacturable as separate components. Car and truck manufacturing is increasingly only a final assembly process, where workers add parts made by contract manufacturers to a vehicle’s frame as it rolls down the line. And in fact, wire harnesses are among the very first components added to the nascent vehicle, which is both evidence of their importance to the finished product as well as explaining how difficult it can be to access some of them if they need to be serviced later.
The design of a wire harness starts pretty much the way any complex circuit design starts: with a schematic. In most modern vehicles, pretty much everything talks to one or more of perhaps dozens of electronic control modules, scattered around the vehicle to control everything from ignition timing and fuel injection to HVAC controls and infotainment system settings. Wire harnesses must be designed for each ECM, to provide power and data connections to each sensor and actuator, with consideration given to sizing the wire for the load, providing appropriate ground connections, and making sure the proper connectors are used.
Interdimensional Design
While the initial design process of a wire harness can use more or less standard EDA tools, eventually the two-dimensional schematic representation of the harness has to be translated to the three-dimensional structure of the vehicle. For that job, more specialized EDA and CAD tools are employed. A big player in this world seems to be CATIA by Dassault Systèmes, which has the tools needed to not only create the 2D schematic but to translate it into the 3D space of a vehicle chassis. These tools allow the designer to create bundles of wires, add connectors, define branches off of the main bundle, set the paths over which each bundle will be laid, and look for any contentions between the harness and the rest of the structure of the vehicle. They also allow the designer to specify how the wires are going to be bundled together — tape wrap versus wire loom, for example — and where and how the harness will be attached to the vehicle.
Physical restraint of the harness brings up another important design consideration: slack. Building the correct amount of slack into each bundle and branch of a wire harness is critical. Too much slack is wasteful, both in terms of the copper needed for the extra wire and in terms of decreased fuel efficiency thanks to extra weight. Excess slack can also lead to physical damage to the harness thanks to abrasion on the vehicle body or frame members, or by snagging on road hazards or even being stepped on by passengers. Insufficient slack is a problem, too — wires that don’t have some give may stretch and break as the vehicle frame twists and flexes, and wires that are too tight may make it difficult to undo connectors for repairs. Harness EDA tools are capable of calculating the right amount of slack for a bundle, and of placing hold-downs and restraints in the right place to make sure the wires flex just enough, but not too much.
Once the 3D model of the harness is finalized, the design has to be translated into something that can be manufactured. And since the main manufacturing methods used for wire harnesses all rely on the use of nail boards — more on which below — the painstaking 3D design has to be flattened back into a 2D drawing. CATIA has automated tools for flattening, with the end result being a 2D drawing that details exactly where each wire in a bundle will go, which pin in which connector it will terminate in, and where and what kind of accessories, like retaining clips, grommets, cable ties, or abrasion protection sleeves, will be added. The output from the flattening process represents a complete set of work instructions that can be sent to a contract manufacturer.
Staying in Good Form
With as automated as almost all manufacturing has become, especially for motor vehicles, where production runs in the hundreds of thousands are not uncommon, you’d think that wire harness manufacturing must be completely automated. After all, how could a contract manufacturer be expected to keep up with the volume of harnesses needed by a modern car plant, especially with lean methodologies and just-in-time production? Surely there must be massive CNC machines that use the work instructions to spool out wires and bundle them all together — right?
Wrong. After the design phase, almost all wire harness manufacturing is strictly a hands-on enterprise. As it turns out, human dexterity and eye-hand coordination are really hard to match with robots. Wire harness plants employ thousands of workers to hand-assemble almost every piece of a wire harness. Yes, there are tools to help, but most of them are used to cut, strip, terminate, and coil up wire that will eventually be used by the human workers to build the harness, one wire at a time.
The traditional way of building a wire harness is on a nail board. Also called a form board or harness board, this is essentially a large flat surface to which are attached a variety of fixtures to temporarily hold wires and connectors. The fixtures are laid out to represent the flattened design of the harness, and instructions printed on the board show which wires are to be routed where. Boards are usually worked on vertically, leaning back at a slight angle to keep wires from falling off before they’re secured.
One worker rarely makes an entire wire harness. Instead, a chain of identical nail boards is looped around the factory floor on a powered carousel, slowly and constantly moving from one worker to the next. Each worker adds a specific set of wires to the growing harness before the board moves along to the next worker with a different set of tasks. In addition to placing wires, some workers are responsible for securing bundles with cable ties, adding protective sleeves, or wrapping the parts of the bundle in loom tape.
It’s these fine motor skills that make full automation of wire harness manufacture a difficult proposition. Threading wires through a length of plastic wire loom is a trivial task for most humans, but would be difficult to build a robot to do. It’s worth noting, however, that this is true mainly because there are plenty of people willing to do such work for relatively low wages. Companies like Yazaki, which currently has about 30% of the global market of wire harness production, employ hundreds of thousands of people around the world, particularly in developing areas. Economic forces currently favor the continuation of this model, but as we’ve seen time and again, eventually everyone wants to be able to buy the stuff they’re making for other people, so the supply of workers willing to do this kind of work for low wages is limited. Perhaps then it’ll make sense to invest in full automation up and down the wire harness production chain.
0 Commentaires