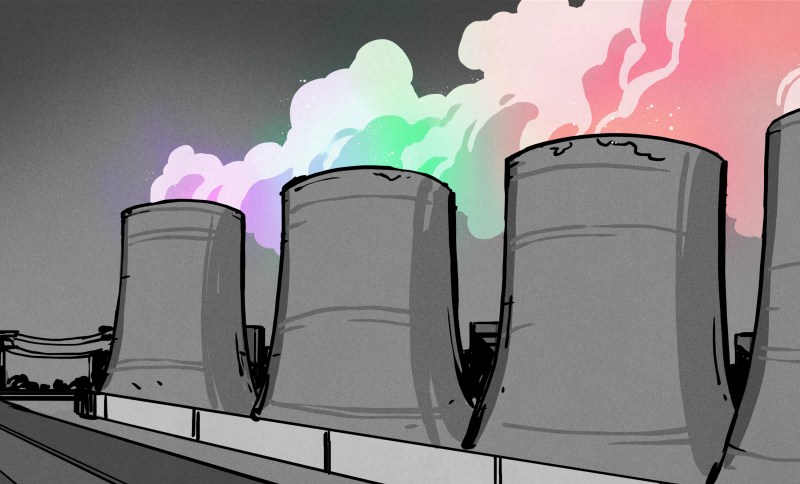
All nuclear fission power reactors run on fuel containing uranium and other isotopes, but fueling a nuclear reactor is a lot more complicated than driving up to them with a dump truck filled with uranium ore and filling ‘er up. Although nuclear fission is simple enough that it can occur without human intervention as happened for example at the Oklo natural fission reactors, within a commercial reactor the goal is to create a nuclear chain reaction that targets a high burn-up (fission rate), with an as constant as possible release of energy.
Each different fission reactor design makes a number of assumptions about the fuel rods that are inserted into it. These assumptions can be about the enrichment ratio of the fissile isotopes like U-235, the density of individual fuel pellets, the spacing between the fuel rods containing these pellets, the configuration of said fuel rods along with any control, moderator and other elements. and so on.
Today’s light water reactors, heavy water reactors, fast neutron reactors, high temperature reactors and kin all have their own fuel preferences as a result, with high-assay low-enriched (HALEU) fuel being the new hot thing for new reactor designs. Let’s take a look at what goes into these fuel recipes.
Gathering Ingredients
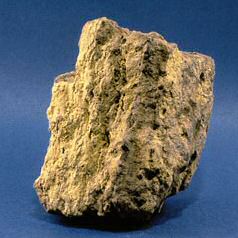
The raw ingredients are usually mined from the ground, with the mining of uranium from seawater a relatively new development. The countries with the most uranium ore available for extraction are Australia (28%), Kazakhstan (15%) and Canada (9%), with Canada having the highest-grade uranium ore. Generally, the product from uranium mines is U3O8, which contains about 85% uranium. The next step depends on whether the natural uranium has to be enriched, meaning the amount of fissile (U-235) material increased from the naturally occurring level.
Once at a fuel manufacturing plant the original natural uranium will be in one of two forms, either uranium hexafluoride (UF6) or uranium trioxide (UO3), with the former being the case when enrichment has taken place. Before this can be turned into fuel pellets, this form will need to be converted to uranium dioxide (UO2). These pellets are what is usually referred to as ceramic fuel pellets, which contrasts with the more rarely used metallic fuel types (e.g. ZrU) that saw use in some reactors until the 1980s. A major advantage of UO2 ceramic pellets is the high melting point of 2,865°C, which is a good property for the high-temperature environment of a nuclear fission reactor.
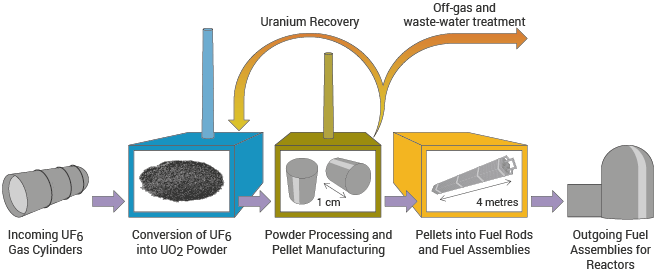
The ceramic fuel pellets are produced under several hundred MPa of pressure, after which they are sintered at 1,750°C under an oxygen-free atmosphere (usually argon-hydrogen). The sintered pellets are then machined as a final step. This gets them to the exact dimensions required to fit into the fuel rods, with any removed material returned to an earlier part of the pellet manufacturing process. For most reactor types these pellets are roughly 1 cm in both diameter and length.
An interesting addition to some pellets can be a burnable neutron absorber such as gadolinium (in oxide form), that is added to remove neutrons early on in the fuel cycle, thus reducing reactivity and allowing for longer fuel life. More commonly, zirconium diboride is added as a burnable absorber in the form of a thin coating on pellets. This is used in most US reactors, including the AP1000 type (and derivatives) that is also used in China.
Packing It Up
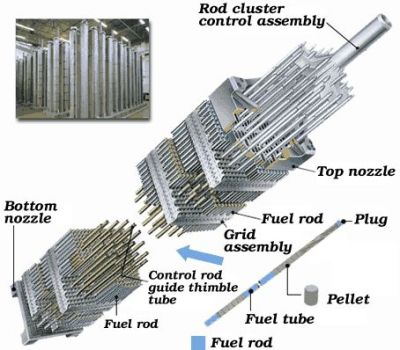
The fuel rods themselves are generally made out of a zirconium alloy, which has the beneficial properties of having a high melting point, high resistance to chemical corrosion, vibrations and impacts. These alloys are also essentially transparent to neutrons, meaning that they do not interfere in any noticeable way in the reactor’s nuclear fission chain reaction. These fuel rods contain a large number of individual ceramic fuel pellets, which after filling is flushed and ultimately filled with pressurized helium gas at a few MPa. Some space remains between the end caps and fuel pellets that’s usually filled with a spring that provides compression to the stack of pellets.
These individual rods are then fixed in a steel framework, which allows for individual rod types (fuel, moderator, empty slots) to be controlled as required by the target reactor. For an average pressurized water reactor (PWR) type reactor, these fuel assemblies are between 4 m and 5 m tall and 20 cm across. Nearly 200 of these assemblies will go into a 1 GWe PWR, containing around 18 million pellets. While Western fuel assemblies tend to be rectangular, Russian PWR (VVER) reactors use hexagonal fuel assemblies. This does not affect the basic operation, however.
When a PWR is refueled, only about a third or a quarter of the fuel assemblies are removed and replaced with fresh assemblies, with the rest being rearranged to optimize the reactor operation and total burn-up of both the old and new fuel assemblies.
The second most popular type of fission reactor is the boiling water reactor (BWR) design, which as the name suggests directly boils water to create steam, instead of using a pressurized primary loop as with PWR designs. Although BWRs cannot reach the same level of efficiency as PWRs, they are much better at load-following operations, which is due to the water being led in channels through the fuel assembly. As the water both moderates and cools, varying the flowrate changes the energy output.
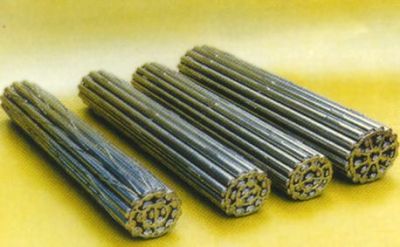
In addition to this, BWR fuel assemblies have a number of other notable differences from PWR fuel assemblies, but none as drastic as with the fuel assemblies for the Canadian CANDU pressurized heavy water reactor (PHWR). This type of fission reactor doesn’t use light water (H2O), but rather heavy water (D2O) that has heavier deuterium instead of hydrogen atoms. This difference enables PHWRs to use unenriched uranium fuel, which are assembled in short bundles that are loaded into fuel channels in the reactor. This loading and unloading can be done while the reactor is running at full power, with unloading happening at the other end of the fuel channel. This means that a PHWR does not have to shut down for refueling or reshuffling of the fuel.
PHWRs are the most flexible fission reactors currently in common use, able to use unenriched, natural uranium, enriched uranium, mixed oxide and other fuels like thorium. They have some overlap with the Soviet RBMK design that can also run on unenriched uranium fuel due to its use of graphite as a moderator, but PHWRs are significantly more versatile.
Exotic Taste
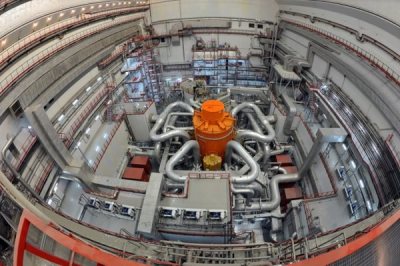
Since virtually all fission reactors in the world today are either a light water reactor (LWR) like the common PWRs and BWRs, or a PHWR (e.g. most of Canada’s reactors), most nuclear fuel produced is some kind of PWR, BWR or PHWR fuel, but there are more exotic reactors that have very different fuel demands yet again. One of these are the fast neutron reactors (FNR), which demand yet another fueling strategy. FNRs generally use the concept of ‘seed’ and ‘blanket’ regions, with the seed regions having high reactivity and neutron production. Neutrons from the seed regions are then captured by the fertile isotopes in the blanket regions, turning them fissile.
FNR fuel is where the once-through uranium fuel cycle of mining-fission-disposal really breaks down, with LWR spent fuel containing significant amounts of fertile isotopes that can be turned into fissile fuel for use by the FNR as well as as fresh LWR fuel. This overlaps somewhat with the traditional reprocessing of spent LWR fuel that removes the uranium and plutonium, allowing for this to be used in mixed oxide (MOX) fuel. MOX fuel is distinct again from REMIX fuel that mixed reprocessed spent fuel with low-enriched uranium.
What is a common factor among all of these fuel types, however, is that they target reactors that run at fairly mundane temperatures. Most recent development has focused on high temperature fuels, for use in high temperature reactors that operate at 750 °C to 950 °C with helium as coolant. The Chinese HTR-PM reactor and US-based X-energy’s Xe-100 design use spherical fuel elements in a pebble bed configuration, which results in a fuel loading and unloading procedure closer to that of PHWRs. China’s aim is to use the so far successful HTR-PM design in an HTR-PM600 configuration — three 200 Watt reactors combined — that can replace boilers at coal plants, which will massively increase demand for this fuel type if successful.
HALEU
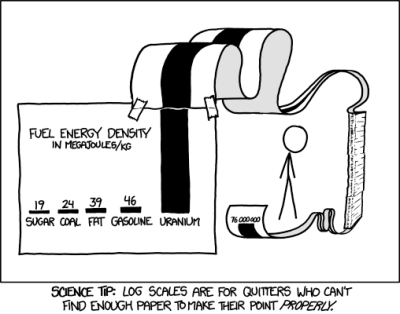
Observant readers may have noticed that over the past years there have been a lot of US-based nuclear power startups that have announced new reactor designs. Many of these require so-called high-assay low-enriched uranium (HALEU) fuel. While the US’s current fleet of fission reactors run on fuel that is enriched up to 5%, HALEU is enriched to between 5 and 20%, which enables more compact designs, higher efficiency and much more time between refueling. This compares to the small reactors in US submarines that run on >90% U-235 high-enriched fuel, granting them their 20-25 year refueling time. Above 20% U-235 is considered to be ‘high-enriched’ (HEU).
Since enriching uranium requires a certain level of production capacity that currently does not exist yet, there is a bit of a catch-up going on in the industrial industry. This has led to for example TerraPower announcing a delay in the start-up of their first Natrium SMR. Previously Russia had been a major supplier of HALEU, but since the war in Ukraine, the reliance has now shifted to the US’s domestic production capacity that is in the process of being rapidly expanded.
Geopolitics aside, what should be clear at this point is the immense variety in nuclear fuel types and their applications, with the new Generation IV reactors adding to this. With an increasing demand for reliable, low-carbon power, it would seem the game is on to extract as much energy as possible from each gram of uranium mined.
0 Commentaires