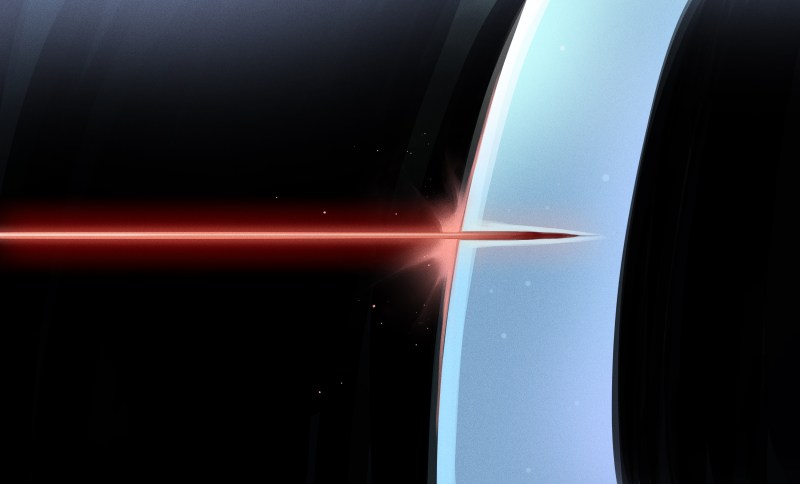
Glass! It’s a finicky thing. Strong as hell, yet chip it and glance at it the wrong way, and you’re left with a bunch of sharp rubbish. It’s at once adored for its clarity and smoothness, and decried for how temperamental it can be in the case of shock, whether mechanical, thermal, or otherwise.
If you’ve ever tried to drill glass, you’ll know it’s a tough errand. To do so without cracking it is about as likely as winning the lottery on Mars. Even lasers aren’t great at it. However, a research team from France has developed a new technique that uses femtosecond lasers to drill microscopic holes in glass with a minimum of tapering and no cracking! Brilliant, no?
Zappin’ Holes
Femtosecond lasers are powerful and useful tools, though they are still obscure enough to require explanation. They are lasers that fire incredibly short pulses, on the order of 1 femtosecond to a few hundred femtoseconds. If you’re unfamiliar with a femtosecond, it’s 1 x 1015 seconds, or roughly one millionth of a nanosecond. These lasers release a great deal of energy in a very short period of time, which, if you do the physics, means high peak power. While these lasers can fire single pulses, they can also be fired repetitively at varying rates. For example, some femtosecond lasers can fire repeated ultrashort pulses at a rate of gigahertz.
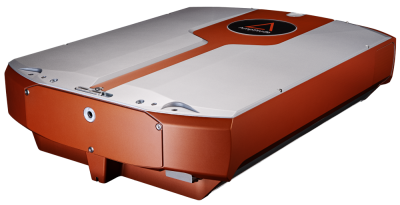
What these lasers offer is the ability to deliver high-intensity pulses of light energy very precisely. This makes them highly useful for very fine, very delicate tasks that involve destroying very small amounts of material in what scientists call ablation. The high intensity pulses are capable of ablating many materials, while the short duration of the femtosecond pulses means that there is minimal thermal impact on surrounding areas. In this way, femtosecond lasers have proven useful for everything from laser eye surgery to various micromachining tasks.
When it comes to drilling holes in glass, though, femtosecond lasers have traditionally performed poorly. Usual techniques involve single femtosecond pulses spaced out by a large stretch of time. This tends to create holes with limited penetration that can also exhibit significant tapering and a rough inner surface. The new method is the work of researchers from the University of Bordeaux. It instead relies on femtosecond pulses fired in gigahertz bursts to drill micro-holes in glass.
As per the research paper, this technique machines far better microscopic holes in glass. Researchers were able to produce deep crack-free holes with an aspect ratio of up to 37:1 in sodalime glass, and up to 73:1 in fused silica. The holes themselves measured just 27-52 μm in diameter, while reaching from 510 μm to 1620 μm deep. In the case of fused silica, the surface finish of the holes was of remarkable quality, too – being “glossy and almost transparent” University of Bordeaux professor Inka Manek-Hönningerto told Photonics Media.
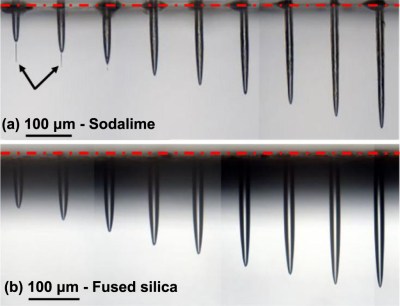
The team used a Tangor 100 laser from Amplitude in the study, a Ytterbium-doped femtosecond laser. The laser output a maximum average power of 100 W at 1030 nm, firing 500 femtosecond pulses. To drill the holes, the laser fired bursts of fifty 500 fs pulses at a repetition rate of 1 GHz. Each burst of fifty pulses lasted 50 nanoseconds. The bursts were then repeated at a rate of 1 KHz. This provided enough time in between bursts for heat to dissipate, which avoided the creation of a heat-effected zone in the material surrounding the holes. The team notes that non-linear absorption behaviours and the cumulative thermal effects of the laser bursts are key to creating the high-quality holes. With the repetitive intense bursts, the ablation rate of the material is increased, helping to produce the deeper, neater holes.
The hope is that the technique could prove useful for various industrial applications. The speed of the technique is limited, to avoid damaging the glass by thermal effects. However, if there’s an application that requires very tiny holes nicely machined in sodalime or fused silica, this technique could be just the ticket. Given that it uses off-the-shelf, albeit advanced, laser hardware, it should be readily reproducible by other laboratories.
0 Commentaires