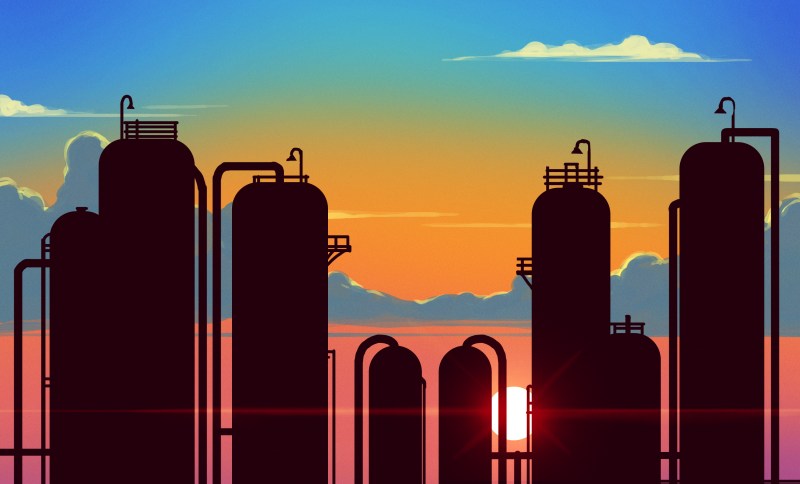
Generally, when we talk about the production of hydrogen, the discussion is about either electrolysis of water into oxygen and hydrogen, or steam methane reforming (SMR). Although electrolysis is often mentioned – as it can create hydrogen using nothing but water and electricity – SMR is by far the most common source of hydrogen. Much of this is due to the low cost and high efficiency of SMR, but a major disadvantage of SMR is that large amounts of carbon dioxide are released, which offsets some of the benefits of using hydrogen as a fuel in the first place.
Although capturing this CO2 can be considered as a potential solution here, methane pyrolysis is a newer method that promises to offer the same benefits as SMR while also producing hydrogen and carbon, rather than CO2. With the many uses for hydrogen in industrial applications and other fields, such as the manufacturing of fertilizer, a direct replacement for SMR that produces green hydrogen would seem almost too good to be true.
What precisely is this methane pyrolysis, and what can be expect from it the coming years?
Carbon Waste
Methane (CH4) is most commonly found as the primary constituent of natural gas and is also prevalent as the output from methanogenesis, which includes the famous cow burps. With steam methane reforming and similar processes, the goal is to strip the hydrogen atoms from the single carbon atom, releasing the hydrogen for capturing. This leaves the carbon as essentially a waste product, that with SMR results in each carbon atom capturing two oxygen atoms to form carbon dioxide, our all too familiar greenhouse gas.
The basic reaction of SMR is given as:
CH4 + H2O ⇌ CO + 3 H2
This is an endothermic reaction, meaning that an SMR reactor is kept within a temperature range of approximately 800 – 900 °C in order for it to actually produce any significant amounts of hydrogen. The aforementioned CO2 shows up in in the additional Water-Gas Shift Reaction (WGSR), described as:
CO + H2O ⇌ CO2 + H2
The point of the WGSR is to extract additional hydrogen, increasing the overall efficiency of the SMR process. Additionally, catalysts are used to increase the efficiency of the reactions, resulting in an overall efficiency of SMR up to 75%.
The capital costs for an SMR installation are rather minor, with the continuing costs being primarily the natural gas feedstock and fuel for the heating of the reactor. If the produced carbon monoxide and carbon dioxide also have to be captured (so-called ‘blue’ hydrogen’), the capital and ongoing costs are going to be correspondingly higher and system efficiency lower (~60%). This makes carbon capture and storage with SMR economically unattractive, and is where ‘turquoise’ hydrogen produced using methane pyrolysis.
Turning Up The Heat
The main difference between SMR and methane pyrolysis is the temperature. It employs the thermal decomposition of methane, with temperatures of generally well above 900 °C, with some approaches explored over the decades suggesting up to 1,900 °C. A general issue with methane is that it is a very stable molecule, owing to its C-H bonds.
As a result of these strong bonds, thermal decomposition of methane without the presence of a catalyst generally won’t take place until a temperature of over 1,100 °C. The challenge over the past decades of research has been to find a suitable catalyst. Here metal catalysts have been mostly studied, including iron and nickel. A big issue with metal catalysts is their rapid deactivation through the formation of carbon deposits on the surface. Reactivating the catalyst by cleaning away the carbon deposit is problematic, and can result in the production of carbon dioxide.
Carbon catalysts have seen more research the past years, with a number of promising advantages making them rather appealing. Usually in the form of activated carbon and carbon black, their advantages can be summarized relative to metal catalysts as follows:
- Lower cost
- Better (thermal) stability
- Tolerance to impurities (e.g. sulfur in the natural gas)
- No need to regenerate the catalyst
- End product is pure carbon, without metals
- The catalyzed carbon deposit may still act as catalyst
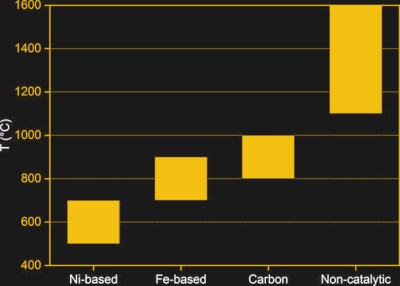
A final, and very different, approach involves molten metals and salts, both in liquid bubble column reactors. In these columns of molten materials, the methane is introduced at the bottom, where the methane thermally decomposes inside the bubbles of natural gas. Once these bubbles reach the surface of the column, the hydrogen and carbon are released, with the lighter hydrogen separating from the carbon that remains suspended on top of the molten salt or metal.
These bubble column reactors would provide a rather ideal, continuous process where the carbon can be scooped off the surface without contaminating the molten material or the produced hydrogen. Currently, however, the research is still ongoing to find the right kind of salt or metal that would work for such a reaction column that would also accept the high operating temperatures.
This means that for the moment, carbon catalysts seem to be the best way to produce hydrogen from methane with pyrolysis, except for the higher temperature range required.
Prime Time Prep
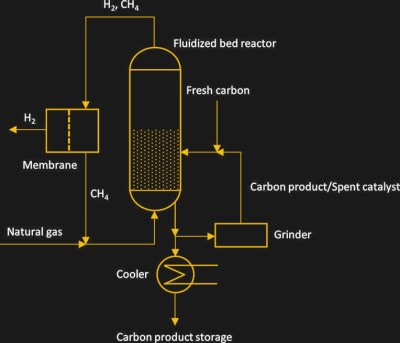
Although an advantage of methane pyrolysis is that today it can reach similar efficiencies as SMR with CCS, creating industrial-scale reactors that can run continuously without constant downtime for maintenance is still an ongoing challenge. A promising reactor type here is the fluidized-bed reactor, along with packed-bed reactors.
Despite the challenges with methane pyrolysis, it nevertheless would seem that its time has come. Today over 95% of hydrogen is produced with SMR. If the free release of carbon dioxide into the atmosphere is no longer acceptable, alternatives like methane pyrolysis have a fighting chance in the hydrogen production market. Of course there are many more ways to produce hydrogen, all with their own advantages and trade-offs.
A real concern is that many of these technologies require either a lot of electricity, or high temperatures. As noted by Sánchez-Bastardo et al., renewable energy is not likely to provide anywhere near the amount of electricity needed for electrolysis of water, even for just industrial demand. Simultaneously, thermal decomposition as with methane pyrolysis requires a source of thermal energy, which ultimately factors into the final cost picture and carbon footprint of the produced hydrogen.
This is where potentially Generation IV nuclear reactors may play a pivotal role, with the VHTR type (high-temperature, helium-cooled) providing an outlet temperature of 900 – 1,000 °C, which would be sufficient for methane pyrolysis. One such VHTR – China’s HTR-PM – is intended to be used for hydrogen production, in addition to electricity production.
One thing that does seem to be quite certain, however, is that hydrogen production will become a lot greener, with more and more carbon from methane scooped out of pyrolytic reactors rather than released into the atmosphere attached to oxygen atoms.
0 Commentaires