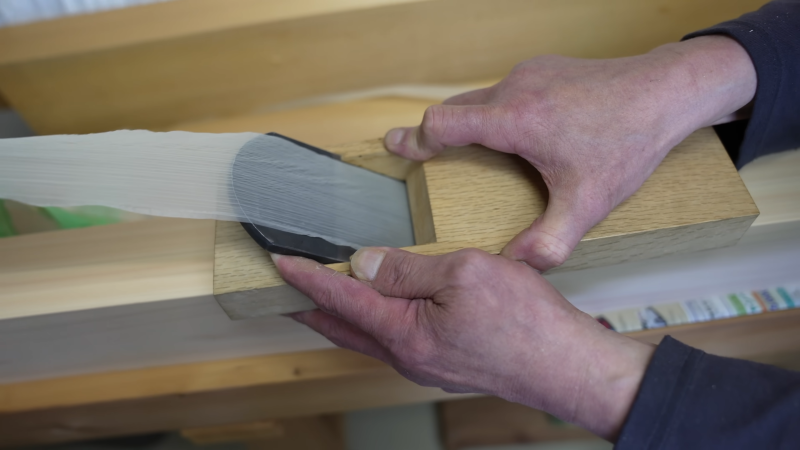
If you’re a woodworker, you know the value of a good planer. A stout model will last a lifetime if properly cared for. [Process X] has now taken us behind the scenes of a Japanese factory that turns out quality planers to show us how it’s done.
The video starts at the forge, where steel is attached to soft iron to form a blank that will become the planer blade. This is proper blacksmithing, with autohammers and flames akimbo. It’s also a woodworking story, though, with the planer bodies themselves carefully prepared for the years of faithful service ahead. We get to see the raw wood roughed into shape and put through the thicknesser, along with the more interesting machining steps that carve out the angled pockets and the blade slot.
The final assembly is great, too, particularly when the pins are nailed in to hold everything in place. The test is the icing on the cake, in which the planer peels a perfect contiguous strip from a long piece of lumber.
It’s still very much a manual process, with the workshop largely relying on classical machine tools. There’s not a hint of CNC control to speak of. For the Komori Planer Factory and the Koyoshiya Watanabe Woodworking Shop, though, the old methods are doing just fine.
Thanks to [Keith Olsen] for the tip!
0 Commentaires