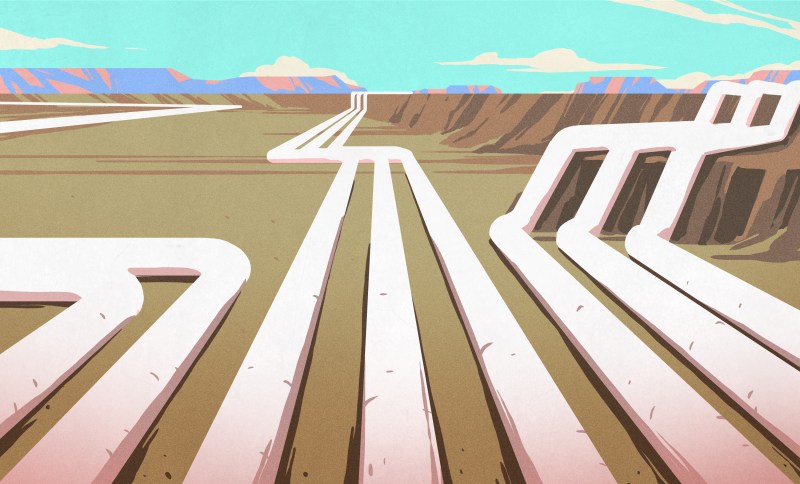
When someone talks about “The Grid,” as in “dropping off the grid” or “the grid is down,” we tend to think in terms of the electromagnetic aspects of the infrastructure of modern life. The mind’s eye sees The Grid as the network of wires that moves electricity from power plants to homes and businesses, or the wires, optical cables, and wireless links that form the web of data lines that have stitched the world together informatically.
The Grid isn’t just about power and data, though. A huge portion of the infrastructure of the developed world is devoted to the simple but vital task of moving liquid fuels from one place to another as efficiently and safely as possible. This fuel distribution network, comprised of pipelines, railways, and tankers trucks, is very much part of The Grid, even if it goes largely unseen and unnoticed. At least until something major happens to shift attention to it, like the recent Colonial Pipeline cyberattack.
A Series of Tubes
This story actually started a week before the pipeline attack while I was filling up some gas jugs at the local filling station. There was a tanker truck parked in the lot, dispensing gasoline and diesel into the buried storage tanks through big hoses. Any driver is likely to have witnessed a scene like this before without giving it a second thought, as I had many times before. But it struck me this time that I had no idea where that tanker truck had filled up before heading out on the morning rounds. Where I live in North Idaho, the nearest seaport — a logical place for gasoline and other fuels to arrive by tanker from refineries located in other parts of North America — is a six-hour drive away. Would a truck driver really be asked to drive that far to pick up and then deliver fuel?
As it turns out, the tanker trucks that we all see topping off the tanks at gas stations are only the very last link in the petroleum transport network, and tanker trucks in general play only a small role in the fuel distribution system. The network is divided into two main functions: getting crude petroleum from where it’s produced to where it can be processed into finished products, and getting the finished products to the customers. While surface transportation, especially oil tankers, play an outsized role in moving crude oil around, the finished products network is dominated by pipelines.
In the United States, there are close to 200,000 miles (322,000 km) of oil pipelines, the bulk of which is dedicated to moving finished products from refineries to consumers. Some of these stretch vast distances, like the 5,500 miles (8,900 km) that the Colonial Pipeline covers on its way from the refineries of Texas through the major cities of the southeast and Eastern seaboard through to its terminus outside of New York City in Linden, New Jersey. The twin pipelines, with one devoted mostly to moving gasoline and a smaller one used for other products, like diesel and jet fuel, move a total of three million barrels (126,000,000 gallons or 477,000,000 liters) of product every day.
Pipelines move oceans of petroleum products around every day, and criss-cross the country in an intricate web of infrastructure. And yet, almost all of this vast network is invisible, buried safely below ground for the majority of its length, surfacing only occasionally at pumping stations, control points, and tank farms. Pipeline construction itself is a fascinating subject; a pipeline is much more than just a buried pipe, and an immense amount of effort and engineering goes into building one.
Mix and Mingle
Once a finished products pipeline is built and tested, it begins the non-stop work for which it was designed. Like trucking companies, shipping lines, and railways, pipeline companies are what’s known as common carriers, which means they have to accept shipments from anyone who meets their published specifications. They don’t generally own the product that’s being shipped, but rather contract with the products’ owners to move it from one place to another. This means there are almost always products from more than one refiner in a pipeline at any time, queued up along the length of the pipe.
In addition to a mix of product owners, each shipper will likely have a variety of products in the pipe at any one time. The most common example is the different grades of gasoline, which in the United States basically means different octane ratings and varying amounts of ethanol. These all travel in the pipeline in sequence, immense slugs of each product nestled up against each other. There will necessarily be some mixing of products that occur in transit, resulting in what’s known as intermix zones. Product from intermix zones needs to be treated differently from the “clean” product in the middle of the bolus. In the case where different grades of gasoline are intermixed, the receiving tank farm generally puts the mixed product into the storage tank for the lower of the two grades, on the theory that it’s better to sell a slightly higher grade of fuel than is being advertised. When different products, like gasoline and diesel, get intermixed, the receiving facility has to segregate the intermixed products and send the unmarketable cocktail back to the refinery for reprocessing.
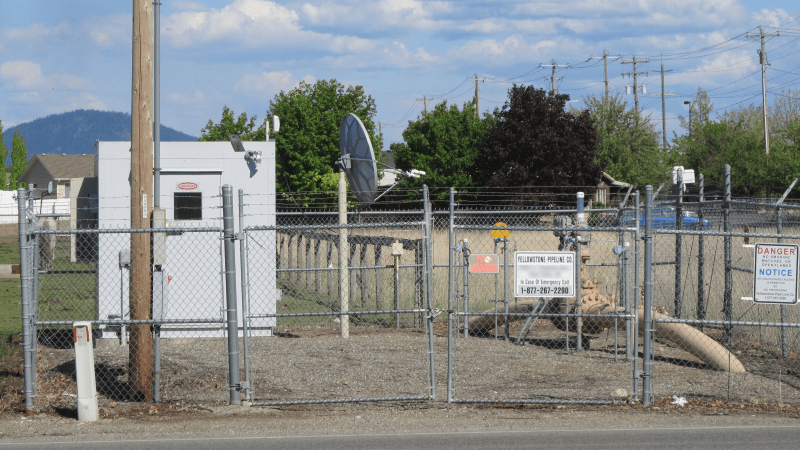
In either case, the state of the product in transit and the overall health of the pipeline are monitored by a far-flung array of sensors. Determination of which product is at which point in the pipeline is normally the business of specific gravity sensors, which continually sample the density of the product as it moves along in the pipe. Pipelines also routinely monitor pressure, temperature, and flow rate along their length, as well looking for leaks and any sign of intrusion into any of their above-ground facilities. These sensors, along with actuators on valves that control the flow, are remotely controlled by the pipeline operators through a SCADA, or supervisory control and data acquisition, network.
Down on the Farm
At the terminus of most pipelines, and sometimes at points along the way, are located one of their more recognizable above-ground features: the tanks farms. Also known as oil terminals and varying in size from just a few small storage tanks to dozens or hundreds of towering structures, tank farms serve as a rest stop for finished petroleum products on their journey from refinery to filling station. Tank farms can also serve as junctions between two or more independent pipelines; for example, in my area, finished products are shipped from refineries in Utah in a pipeline that terminates in Spokane, Washington. The tank farm there serves the entire eastern Washington and Idaho Panhandle region; another pipeline starts at the Spokane terminal and extends east over the Rocky Mountains to an oil terminal in Thompson Falls, Montana, which serves the entire western region of that state.
Each oil terminal will have the pumping gear and valves needed to divert the pipeline’s flow into different storage areas, so that the incoming products from different manufacturers can be segregated before being shipped to customers. Different tanks are available to store the different grades of fuels, too, as well as for the intermix products that need to be shipped back to the refinery. Most oil terminals do very little in the way of manufacturing; products generally arrive there ready to be sold to consumers. Some terminals do perform a limited amount of blending, though, and some may even add ingredients such as ethanol as seasonal needs dictate.
As efficient as pipelines are at moving products around, it’s important to note that they’re not universal. There are vast stretches of North America that aren’t serviced by any pipelines, particularly in the western areas of the United States where population density can’t support the investment needed. The northeast US also lacks many pipelines, but for the exact opposite reason — population density makes it hard to get right-of-way to build pipelines. There, other modes of transportation have to suffice; in New England, for instance, the oil terminals in New Jersey fill up barges with finished products, including the all-important home heating oil, which then head up Long Island Sound to fill the tanks of oil terminals in cities all along the coast.

On the Road Again
Finished products generally don’t spend much time in the tank farms of an oil terminal. From the pipeline operator’s perspective, storage space in an oil terminal is a limited resource, and clearing out tanks to make room for new products coming up the pipeline is critically important. From the products’ owners viewpoint, they can’t make any money until the product is delivered to a retailer. So, it’s in everyone’s best interest to have a streamlined and efficient process for getting products shipped out of the terminal.
To that end, most terminals are designed to get tanker trucks filled and on the road again as quickly and safely as possible. Tanker trucks are filled from the bottom, with the vapor phase of the volatile liquids recovered for recycling. Each tanker is usually divided into multiple compartments, so that different grades of gasoline can be loaded — in the United States, diesel is never carried in the same tanker as gasoline, so an entirely different tanker is used to deliver diesel gas stations.
The total time that finished petroleum products spend in transit from refinery to customer varies, but is primarily a function of how long it spends in the various pipelines along the way. In the case of the Colonial Pipeline, under normal circumstances it takes about five days for a product to make it from Houston to New York. So in most cases, thanks to the efficiency of the fuel distribution network, the fuel you’re filling up with today was probably refined no more than a week or so ago, and has spent most of its short life in the pipe.
0 Commentaires