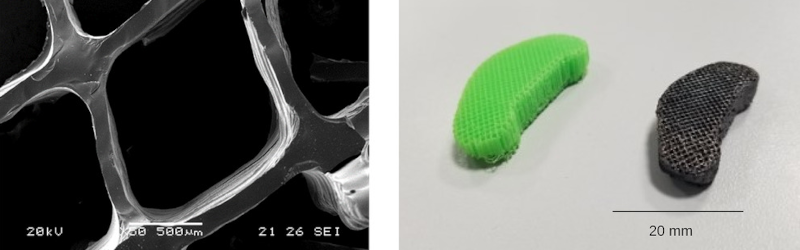
Creating things with ceramics is nothing new — people have done it for centuries. There are ways to 3D print ceramics, too. Well, you typically 3D print the wet ceramic and then fire it in a kiln. However, recent research is proposing a new way to produce 3D printed ceramics. The idea is to print using TPU which is infused with polysilazane, a preceramic polymer. Then the resulting print is fired to create the final ceramic product.
The process relies on a specific type of infill to create small channels inside the print to assist in the update of the polysilazane. The printer was a garden-variety Lulzbot TAZ 6 with ordinary 0.15mm and 0.25mm nozzles.
The process doesn’t sound quick. After printing, the part stayed in an acetone bath along with a tiny bit of a platinum-based catalyst for 15 minutes. Then they added the polymer and waited four hours followed by a 24 hour air dry.
The firing was probably not easy to do in a normal kiln, either. The final stage was 1200C for an hour in nitrogen. We don’t know how this would work with more conventional tools and we know the catalyst is a bit pricey. On the other hand, you don’t use much of it. This might be an area for experimentation if you have some experience and tools for working with ceramics.
This is pretty different from the usual approach we see. If you want to roll your own kiln, start here.
0 Commentaires