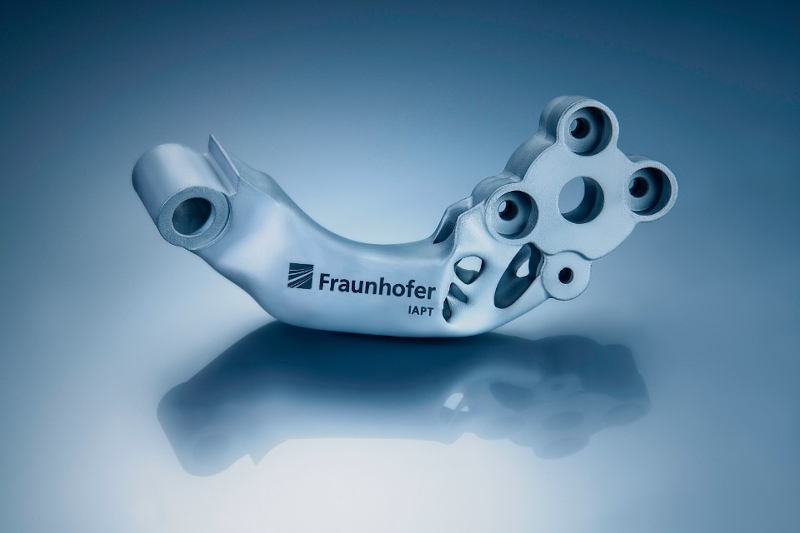
We often use 3D printing to replicate items we might otherwise make with traditional machining methods. Fraunhofer’s new door hinge for a sports car takes a different tack: it tries to be better than the equivalent machined part. The company claims that the new part is half the cost and weighs 35% less than the normal hinge.
Using tools in their 3D Spark software, the team analyzed different factors that led to manufacturing cost. Some of these were specific to the part while others were specific to the process. For example, orienting the part to minimize support and maximize the quantity that fit on the build surface.
By simulating the force on the hinge, the tools could remove material where it didn’t make much difference. This allowed a 35% reduction in weight. Less material also means less print time, further saving costs.
Honestly, nothing they did should be news to anyone involved in 3D printing. Orienting a part in a sensible way makes sense. We’ve seen the removal of unnecessary material both in 3D printing and traditional manufacturing. The interesting part is the use of tools to help automate these optimizations. We can’t tell what the pricing of the software is, and we are guessing it isn’t aimed at the hobby 3D printing market. But it is interesting what can be done and we suspect a little elbow grease and simulation in available software could net similar results.
In theory, any tool that can do finite element analysis ought to be able to determine the material to remove. We’ve noticed carmakers are embracing 3D printing.
0 Commentaires