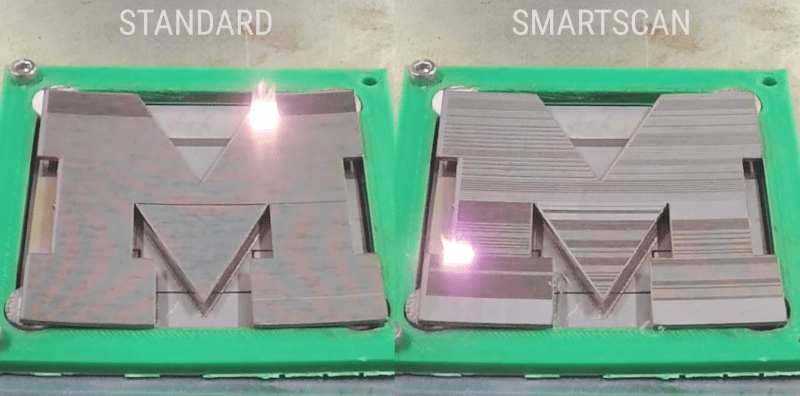
We are used to dealing with warping when printing with thermoplastics like ABS, but metal printers suffer from this problem, too. The University of Michigan has a new technology, SmartScan, that promises to reduce this problem. You can see a video about the technique, below.
The idea is to develop a thermal model of the printed part before laser sintering and then move the laser in such a way that heat doesn’t accumulate. The video shows how engraving metal in the traditional way causes the metal to warp as the laser heats up areas. Using the SmartScan thermal model, they were able to reduce deformation by almost half.
It sounds like they have not yet applied this to sintering in a 3D printer, so you can only assume that the results would be similar. Of course, heat distribution through a powder may well be different than through solid metal, so further testing is certainly warranted.
We couldn’t help but wonder, too, if the results would be almost as good if you simply selected random segments of the pattern to run instead of running totally in sequence. Sure, the model-based approach ought to be better, but we wonder if it would be much better compared to a simple dice roll method.
Meanwhile, we are still waiting for our metal 3D printer. Copper seems to be in reach. If fact, it is, if you don’t mind some postprocessing.
0 Commentaires