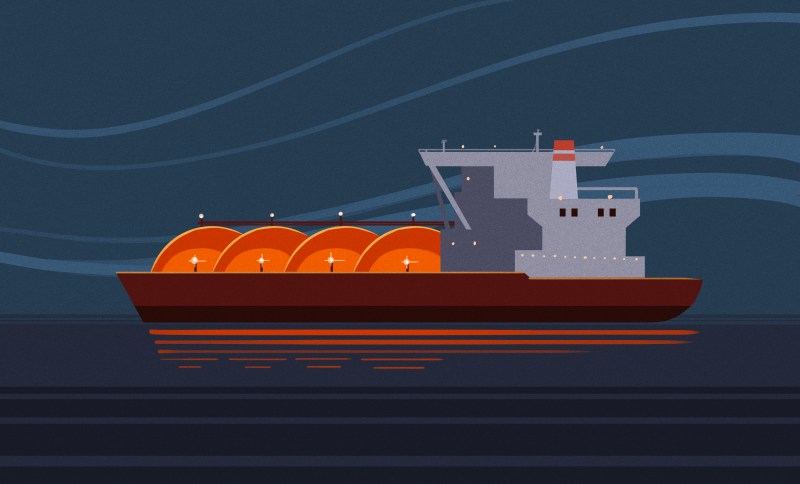
The topic of energy has been top-of-mind for us since the first of our ancestors came down out of the trees looking for something to eat that wouldn’t eat them. But in a world where the neverending struggle for energy has been abstracted away to the flick of a finger on a light switch or thermostat, thanks to geopolitical forces many of us are now facing the wrath of winter with a completely different outlook on what it takes to stay warm.
The problem isn’t necessarily that we don’t have enough energy, it’s more that what we have is neither evenly distributed nor easily obtained. Moving energy from where it’s produced to where it’s needed is rarely a simple matter, and often poses significant and interesting engineering challenges. This is especially true for sources of energy that don’t pack a lot of punch into a small space, like natural gas. Getting it across a continent is challenging enough; getting it across an ocean is another thing altogether, and that’s where liquefied natural gas, or LNG, comes into the picture.
Liquefaction
Before we start looking at how LNG is made, it’s best to start by asking why we even need LNG in the first place. After all, we’ve got an incredibly complex, continent-spanning infrastructure of pipelines that’s optimized for the long-haul bulk transportation of natural gas. Why bother to go through all the effort and expense of liquefying natural gas?
In a word: oceans. Those vast networks of pipelines pretty much stop at the water’s edge, and while there certainly are some undersea natural gas pipelines, recent events have shown us just how vulnerable those can be. So shipping natural gas by sea has become a necessary means of moving energy from point A to point B. And to do that efficiently, you need to dramatically reduce its volume. Turning natural gas into a liquid does exactly that: it increases its density 600 times, making it feasible to ship in bulk.
The feedstock for liquefied natural gas is, of course, natural gas. We’ve already covered a fair amount about the process of harvesting and distributing natural gas, but briefly, natural gas is a mixture of hydrocarbons like methane and ethane produced from the decay of ancient biomass in geological formations. Along with liquid hydrocarbons and contaminants like nitrogen, carbon dioxide, sulfur-containing compounds, and water vapor, the gas accumulates in underground reservoirs that are tapped by drilling.
Raw natural gas is transported, under its natural pressure or with the help of enormous compressors, via pipelines to plants that clean the gas. Recovering sulfur and helium, both valuable chemical elements, from the raw gas is especially important, but it’s also important to scrub low-value contaminants like water and CO2 from the natural gas, since they can both cause freezing problems down the line. Water is removed by bubbling the raw natural gas through triethylene glycol (TEG), an extremely hygroscopic solution, while CO2 is removed using an amine scrubber, which exposes the acidic raw gas to nitrogen-containing amine solutions like diethylamine (DEA), which adsorbs the CO2. After further purification, which removes any remaining heavier hydrocarbons and contaminants like mercury, which will not behave when exposed to aluminum and stainless steel, the natural gas feedstock is about 85% to 90% methane (CH4), with the rest being a mix of ethane (C2H6), propane (C3H8), and butane (C4H10).
The clean, dry natural gas is then ready for liquefaction. Like most gases, natural gas will condense into a liquid when its temperature drops below its boiling point, which is -161.5°C for methane. So, to make LNG, an industrial-scale cryogenic process is required. Most LNG today is made with a process called C3MR, which is a dual-loop progressive cooling system. The “C3” refers to propane, a three-carbon compound used as the refrigerant in the pre-cooling loop. Each half of the cycle is essentially the same as found in any refrigerator, although vastly different in scale. In the precooling stage, liquid propane is passed through an expansion valve, which causes a phase change and a sudden drop in temperature. The cooled propane removes heat from the natural gas via a heat exchanger, the propane is compressed with a three-stage compressor, and the heat is removed via a condenser so the cycle can begin again.
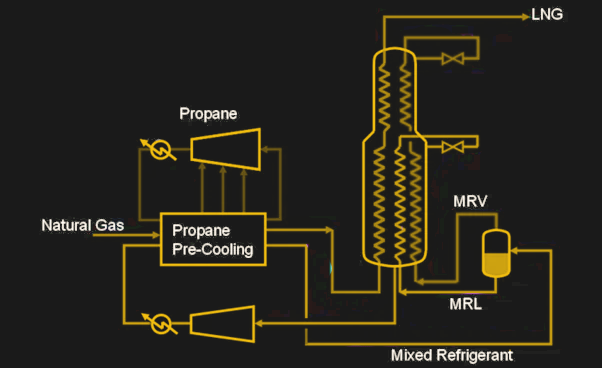
After pre-cooling, the natural gas is at about -33°C — cold, but not cold enough. The cooled gas now enters the “MR,” or “mixed-refrigerant” loop, with a mix of propane, pentane, methane, and ethylene used. Again, the thermal cycle is familiar, but the scale is even more massive — the coil-type heat exchangers used in some MR loops can have thousands of kilometers of tubing coiled up inside them, with a heat exchange area of 40,000 square meters. There are also plate-fin heat exchangers, which have multiple layers of corrugated fins sandwiched between flat aluminum plates. Plate-fin heat exchangers are installed in insulation-filled enclosures called cold boxes. Both types of heat exchangers are usually deployed in parallel assemblies called trains to achieve massive throughput and redundancy.
After the MR loop, the natural gas has dropped to about -160°C and is now a colorless, odorless, non-toxic liquid. The energy input to get to this point has been considerable — something like 13 kilowatts to yield a single tonne of LNG. As of 2021, the global liquefaction capacity was over 450 million tonnes per year, with more capacity still under construction.
Storage and Transportation
But all of this production means nothing without somewhere to put all this LNG. The cryogenic nature of LNG presents certain engineering challenges. While not as cold as liquid nitrogen or oxygen, LNG can still cause steel embrittlement, which is why special alloys of stainless steel are used for LNG piping and tanks. Storage tanks, which are used to hold LNG temporarily between production and shipping, also have to be carefully engineered. These tanks are often built partially or even fully underground; while the subsoil provides insulation that reduces heat transfer into the LNG, the cold can freeze groundwater and cause frost heave underneath the tanks. Storage tanks also have to allow for some boil-off of the LNG, with the resulting natural gas either captured and sold off through regular distribution channels, or piped back to the beginning of the process and reliquefied.
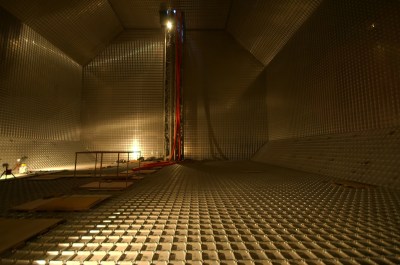
Getting LNG from one place to another is the job of specialized LNG tankers, massive vessels that are purpose-built to safely and efficiently move as much LNG as possible. Although ship designs vary, most of the approximately 550 vessels in the LNG fleet use what’s known as “Moss tanks,” giant spheres that stick up above the deck. Most ships have either four or five of these heavily insulated tanks; while their spherical shape isn’t terribly efficient in terms of using all the volume of the ship’s hull, it does eliminate the danger of cargo sloshing. Newer “prismatic” LNG carriers are being designed, with cargo tanks that more completely fill the hull space. The tanks are lined with an insulated membrane made from either high-nickel stainless steel or the alloy invar, which reduces thermal expansion and contraction. The biggest tankers can hold over 250,000 cubic meters of LNG.
Due to the dangerous nature of their cargo, LNG tankers have to be built with safety in mind. No matter how good the tank insulation is, there will inevitably be some boil-off of the cargo while in transit. Many tankers tap this gas and use it as fuel. The ships also have extensive monitoring systems to detect leaks; unlike natural gas that’s piped to homes and businesses, LNG does not contain methylmercaptan odorant. So methane sensors are located in just about every space on an LNG tanker.
Regasification
Once a cargo of LNG arrives at its destination, it has to be turned back into a gas before being used. The regasification process is basically the opposite of liquefaction, with the LNG being gently heated to above the boiling point. Since the LNG is transported at just below its boiling point, it doesn’t take much of a temperature change to force the phase transition. But that doesn’t mean it’s a simple process.
Regasification can either occur in plants located adjacent to port facilities purpose-built to accommodate LNG tankers, or it can be done by floating storage and regasification units, or FSRUs. FSRUs look very similar to LNG tankers, and have a lot of the same equipment, including ether Moss-type spherical storage tanks or prismatic tanks. FSRUs are also equipped with a regasification plant, which takes the LNG from its storage tanks, passes it through heat exchangers, and pipes the boiled-off natural gas to shore via submerged pipelines. The advantage that FSRUs have versus onshore regasification plants is versatility — there’s no need to wait for favorable tides for an LNG tanker to dock, so offloading can occur whenever the ship arrives.

Whether onshore or floating, the heat for regasification is derived from a variety of sources. Many plants use vaporizers, which heat up the LNG by blowing ambient temperature air over heat exchangers with giant fans. Sometimes, seawater is used as the heat transfer medium, with ambient temperature water sprayed over the heat exchanger coils. Where ambient temperatures are lower, some regasifiers will use submerged combustion vaporizers (SCVs), which have burners submerged in large vats of water. Exhaust gas from the burners heats the water, which in turn heats the LNG as it passes through coils in the tank. SCVs are generally powered by natural gas that’s tapped off from the output.
Once the natural gas is back into its gaseous phase it’s ready to enter the local distribution system. Pipeline operators generally run their distribution systems at 30-80 bar (3,000-8,000 kPa), so the output of the regasifier plant has to match that spec. Rather than compressing the output gas from the regasifier, it turns out to be easier and more efficient to pressurize the LNG input using pumps. The pipeline operator will generally do quality control testing on a batch of LNG before releasing it to its customers, and will of course add in the required methylmercaptan odorant.
The LNG supply chain is pretty complex, but surprisingly energy efficient. Most of the energy goes into liquefaction and transport, with only a little energy needed to push the cryogenic liquid back into a gas. In terms of infrastructure, there’s definitely a lot of that at both ends of the supply chain. But in most cases, the LNG system is the most efficient way to transport chemical energy over vast distances.
[Featured images: Moss-type LNG tanker Arctic Princess. Source: JoachimKohlerBremen, CC BY-SA 4.0.]
0 Commentaires