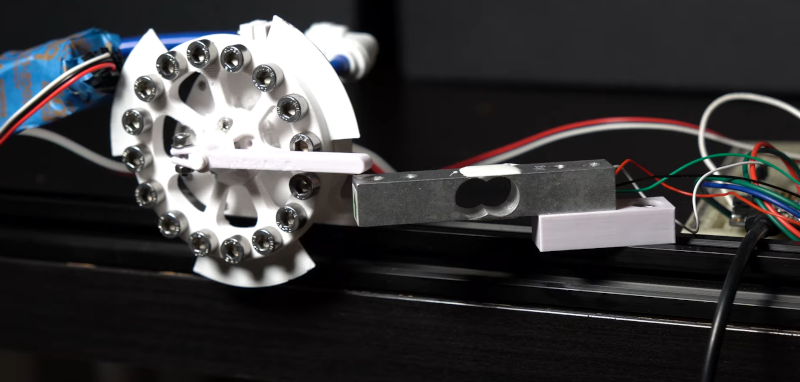
The first video from [3DPrintedLife] attempting to make a liquid piston engine was… well… the operative word is attempting. The latest video, though, which you can see below gets it right, at least eventually.. He has a good explanation of the changes that made the design better. Turns out, one change that made a difference was to turn a key part of the engine inside out. You can see the video below.
The first version would quickly break during operation and while the first new version didn’t work very well, it did stay in one piece which is a definite improvement.
Almost as interesting as the design is the use of fluid simulations and OnShape’s version control to do software-development-like branch and merge to check some of the proposed changes. There’s also a pretty interesting dynamometer design. We also liked the novel method used to visualize airflow — better than smoke.
Finally, what do you do when your 3D printer is down and you need an optical interruption disk for a dynamometer? You’ll see if you watch the video. Not pretty, but we’ve done worse ourselves.
By 12 minutes in, we were worried it wasn’t going to work again, but it did work although it wasn’t terribly reliable to start. Still, when it worked, it worked well and there was plenty of things to learn in the attempt.
Maybe you want to 3D print a jet engine? Or just settle for steam.
0 Commentaires